- Cold storage unit to store carbon fiber
- Clicker and die cutters
- Electric cold press
- Aluminum dies
- Heated press
- Standing ovens
- UV printer
- Grit machine
- Handle molds
- Testing machines
While it cost us time and resources, we knew it would be worth it, and it absolutely was.
As mentioned before, the GT is made right here in the U.S. using American-sourced materials. This allows us to not only ensure a much higher level of quality control but also speed up R&D as everyone working on the GT including the folk physically building out the prototypes have backgrounds in material science, chemical engineering, process engineering, physics, and/or machinery.
We’ve now gotten back to and past the 85% completion mark and on track to release beta units later this month. The official launch is planned for late September.
What is Fusion Foam™?
Let’s talk foam.
Most foam paddles released or teased this year use EPP (expanded polypropylene) - the same polymer used in traditional polypropylene honeycomb paddles. As a result, the difference in feel isn’t as dramatic as you might expect.
Some other paddle companies have experimented with EVA, a foam that offers a noticeably different feel and exceptional power. However, EVA alone typically doesn’t pass USAP deflection testing, which creates challenges for regulation play.
That’s where Fusion Foam™ comes in.
Fusion Foam™ is a proprietary, heat-activated polymeric foam that’s never been used in the pickleball paddle market before. It’s U.S.-sourced and requires custom tooling to activate and shape. Unlike other foams that come in prefabricated sheets and then are cut to size (or sometimes injected), we start from raw material and expand it into the exact shape and density we want.
Here is a photo of fully expanded Fusion Foam in our hybrid shape compared side-by-side to EPP foam:
Spartus Fusion Foam™ Core
|
EPP Foam Core |
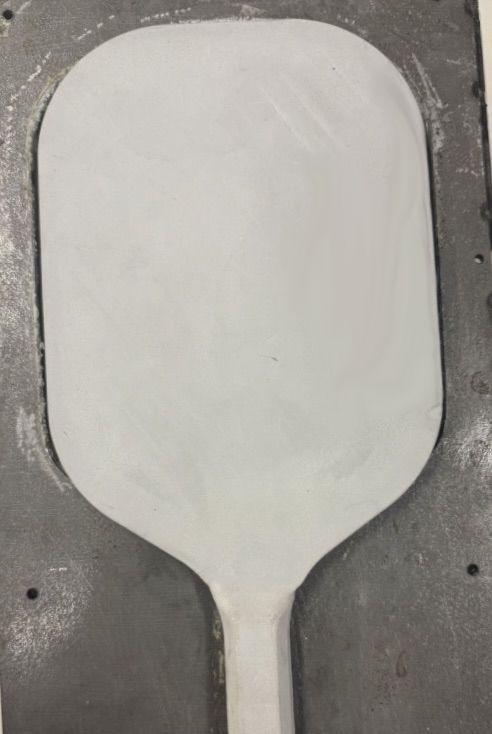 |
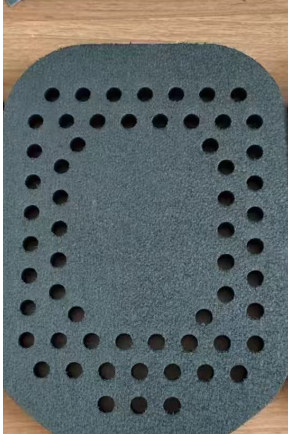 |
EPP foam is readily available from suppliers as a commodity and completely finished EPP paddles are also readily available. EPP is the predominant foam used by other paddle companies because that is the foam being offered by overseas factories, particularly in China.
Here’s an example from Alibaba:
And here’s a close-up showing EPP’s beaded structure, similar to what you’d see in packaging foam. Keep in mind that some companies use different colored EPP such as blue but the general beaded structure will look the same:
Close-up of beaded structure of EPP
|
Packaging made of EPP foam |
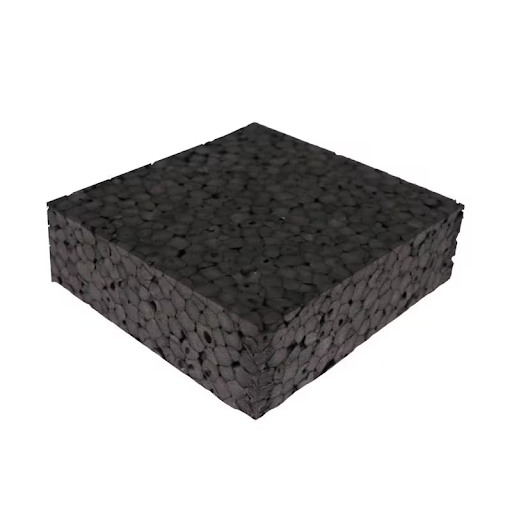 |
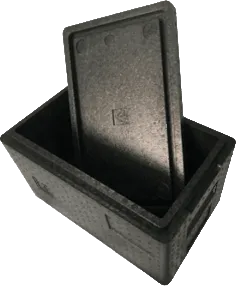 |
While it may be functional, EPP doesn’t deliver the feedback or feel we are aiming for.
Fusion Foam™, on the other hand, is much closer in feel to EVA but with better control and tunability thanks to our unique expansion and shaping process.
How we make the GT
Let’s start with what most paddle construction looks like.
Manufacturers typically cut prefabricated EPP or EVA sheets into paddle shapes. Then, they add face layers, optionally thermoform the body, add shims for the handle, staple buttcaps on, finish it off with edgeguards, grip tape, and printed graphics. In some cases, perimeter foam or other weighting is added prior to the thermoforming step.
The GT is a completely different beast.
To start off, because we created the GTs from scratch, we had to select every material down to ones most people don't even think about. For paddles built overseas, you can customize common components such as how many face layers, what color edgeguards, what materials to use for the face layers, what size honeycombs, etc. but the factories are selecting build materials such as epoxy and resin. For us, we had to select and source every single build components down to epoxies and resins, test them, and retest them if we decided to try other types. This leads to higher quality components being used as we don't use run-of-the-mill materials.
In terms of putting the GT together, our custom equipment transforms raw unexpanded foam material into precise geometries and densities. Face layers, carbon fiber bars, and edge-sealing carbon fiber are added to give the GT both structure and performance.
And then there’s the handle.
Most handles use wood, foam, or plastic shims with a stapled-on buttcap. We designed a fully molded one-piece carbon fiber handle, complete with vibration-dampening materials inside and crisp ergonomic bezels. Once added to the paddle, it becomes one structure from buttcap to paddle head.
The core material and how it is made are both completely new to the market and has never been introduced to the pickleball world as well as our one-piece fully-molded handles. Talk about innovation on innovation.
Our one-piece fully-molded carbon fiber handle
|
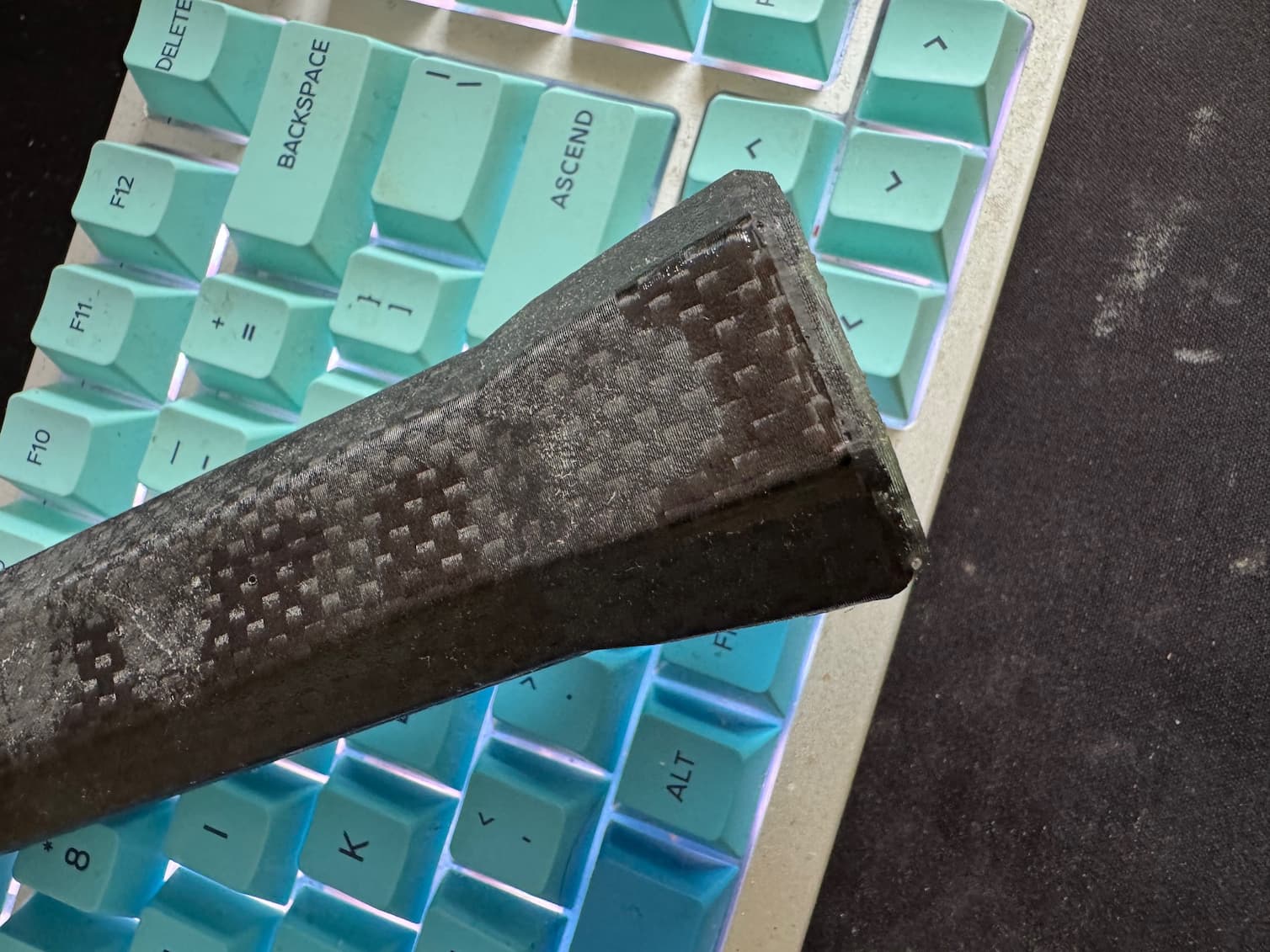 |
Next, graphics are added to the face through UV printing and our patent-pending PermaGrit finish is applied. We’ve received many questions as to whether PermaGrit is a spray on paint - it is not. While PermaGrit looks and feels similar to traditional peel-ply resin grit, it has a special shininess to it, and uses patent-pending chemical engineering to last longer.
We've engaged a design agency for the graphics design and the final design will be different than the design for the betas as shown below.
Close-ups of our PermaGrit
|
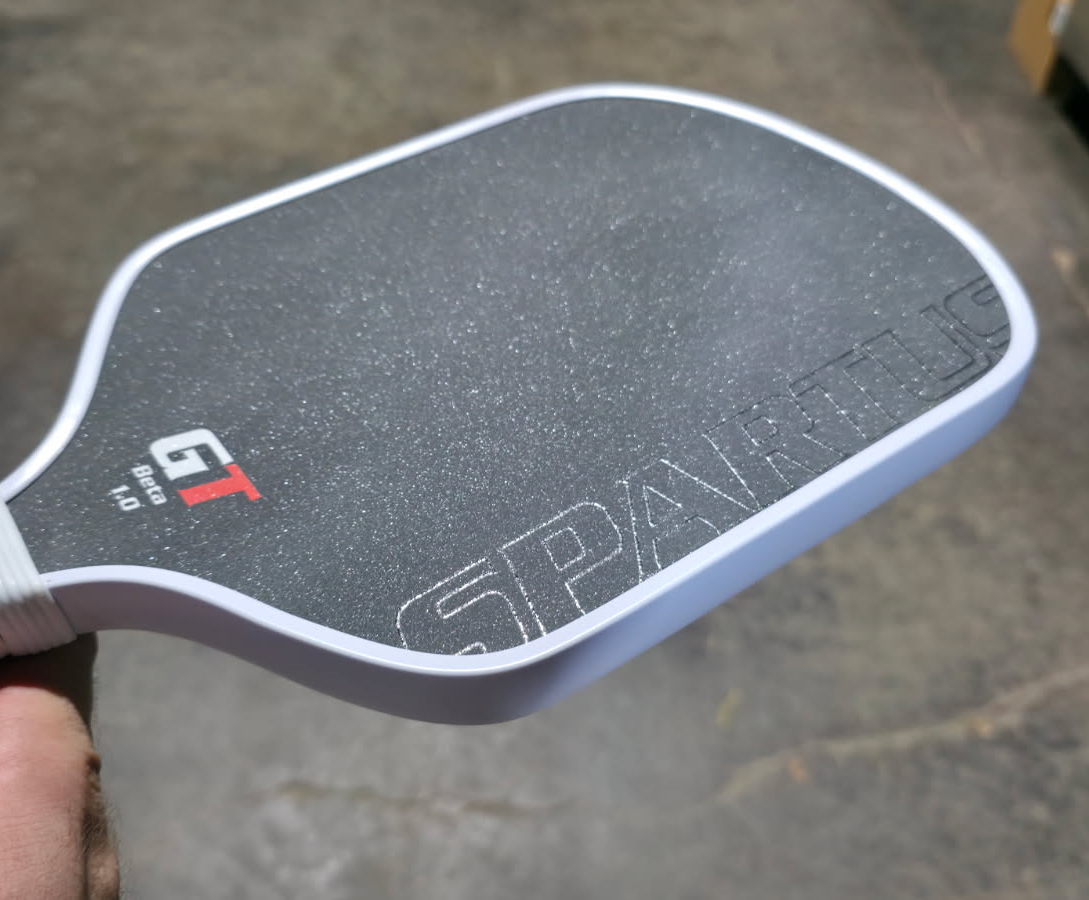 |
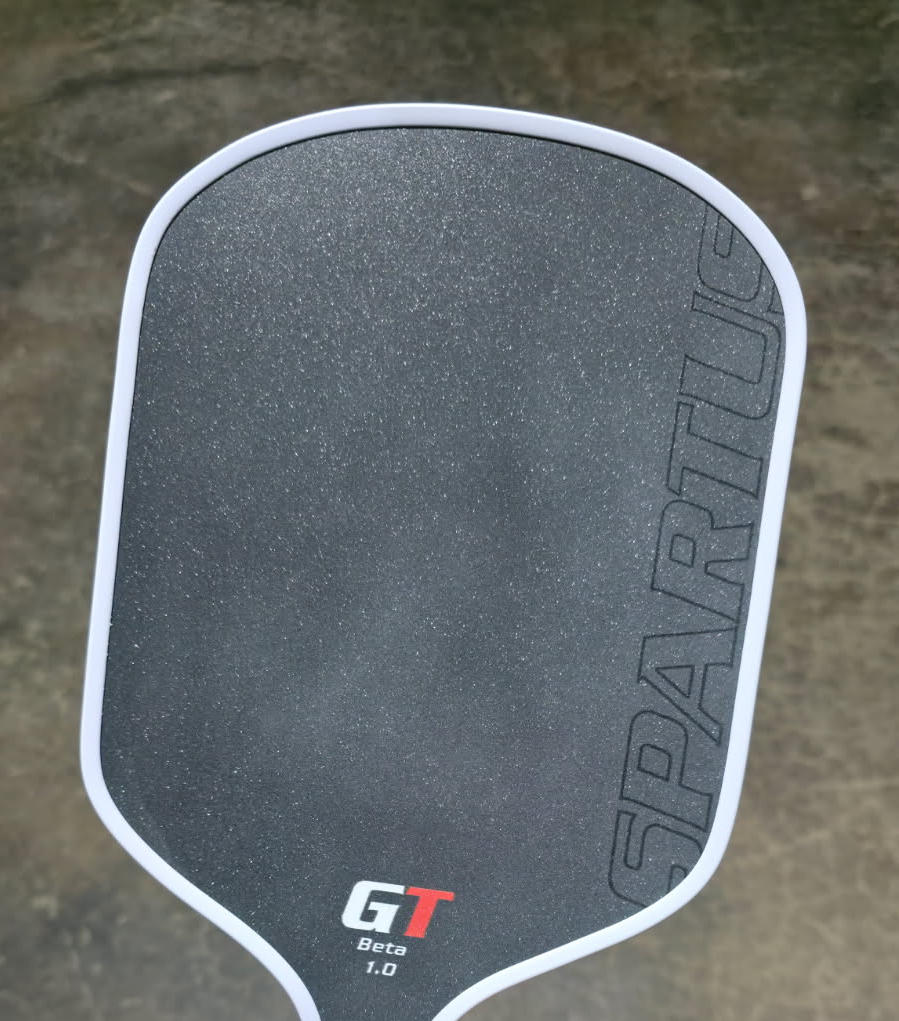 |
Each GT takes 7.5 hours to build starting from the raw material and ending with the edgeguards, grit, and our patent-pending PermaGrit finish.
We’ll share more details about our process in upcoming updates.
How does the GT play?
Here’s what one of the first testers had to say. I was playing in the Los Angeles area with a GT prototype when someone on the courts tried it out. They later posted this in the Pickleball Studio Discord server:
Here is how the GT performs across key areas:
|
Top-tier. There’s noticeable dwell and energy transfer on swings, both partial and full swings. When I say noticeable, it’s extremely noticeable. For comparison, playtesters are coming from power paddles such as the Bantam and Joola IV series.
|
|
This is where the GT really separates itself, especially from other power paddle. Fusion Foam™ gives it a completely different tactile experience than traditional honeycomb paddles. From the first hit, it’s clear you’re playing with something new that has a great feel as if the paddle is wrapping the ball. For those wanting a truly different feel, we believe the GT will be a revelation.
|
|
Because the power is swing-dependent, the GT still delivers great control and finesse for dinks, drops, and resets. The ball doesn’t rocket off uncontrollably on the softer shots.
|
|
Dwell + max grit = massive spin potential. The GT delivers just that. Whether you’re brushing topspin or carving heavy slices, the GT lets you shape the ball tremendously. This spin potential also lasts a long time as our PermaGrit surface holds up to abuse.
|
|
While the 6.8 twistweight is great for a 14mm hybrid, it doesn’t paint a full picture. The dropoff in feel and power going away from the center of the sweetspot is less than normal paddles due to the nature of our Fusion Foam™.
|
Technical specifications in the hybrid shape:
|
|
|
|
|
|
|
|
|
|
|
|
|
|
|
|
|
|
|
|
|
Unidirectional carbon fiber (two layers)
|
|
|
|
|
We'll release the final specs for the hybrid, which shouldn't change much if at all, as well as for the elongated and widebody shapes closer to launch.
A new level of quality
One of the biggest reasons we developed and are producing the GT in the USA is because of our desire to make the highest quality paddles. As many of you know, the pickleball industry has suffered through many quality control issues in the past several years.
By bringing everything in-house and in the States, we are substantially increasing the level of care, attention, and knowledge-based applied to the R&D of the GT as every member of our team working on the technical aspects have backgrounds in material science, chemical engineering, physics, and/or production operations.
The GT was made to overcome many common issues that have been in our industry. First and foremost is core-crushing, commonly called "delamination". Core crushing usually occurs when molds used in thermoformed compress polypropylene honeycombs too much and compromise the sidewalls. Over time, the honeycomb collapses, leading to core-crushing. Because the GT does not use a honeycomb core, there are no sidewalls to compromise and no crushed honeycomb cores.
Second, as mentioned before, our new handle technology is first-of-its-kind and introduces the cleanest and crispest bezels on the market. There are no misaligned shims or incorrectly stapled buttcaps with our handles as you may see in other paddles.
Third, there have been reports of other foam paddles experiencing disbonding between the foam core and face layers from lying in the sun. Because we use high-end, high-temp epoxies with separate curing curves and cure our paddles in accordance to these unique curves, the GT does not carry the same risk of disbonding from sitting in the sun as the curing temperatures are more than double the temperatures of the inside of a closed car in a hot, sunny day.
Finally, because we created every production step ourselves and control the production line, we are able to identify and adjust any ways to make quality control better in real time and quickly.
Since I first started Spartus, my goal has been to create the highest level of quality in paddles and I'm very excited to finally show you the results of this enormous endeavor of making the GT here in the States soon.
A new sub-brand Spartus USA
You may have noticed a new logo at the top of this newsletter. We are introducing a new sub-brand called Spartus USA for our ultra-high performance and innovative paddles made right here in the USA. Spartus USA will include the GT and the upcoming P1. The Spartus USA sub-brand reflects our dedication to innovation, R&D, performance, and quality control. As such, we will be including a much higher level of warranty for Spartus USA paddles, including a lifetime warranty for the GT core.
Our other products will continue to use the heritage Spartus logo.
Heritage Spartus logo
|
Spartus USA logo |
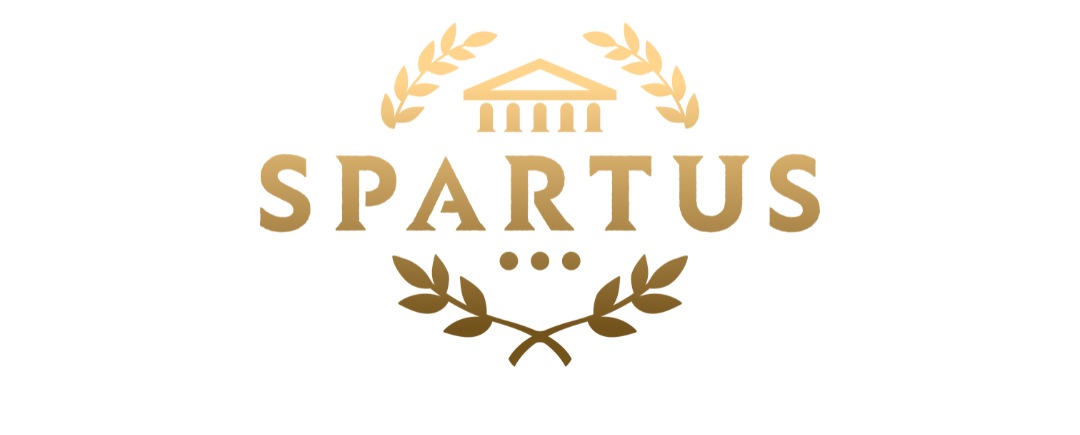 |
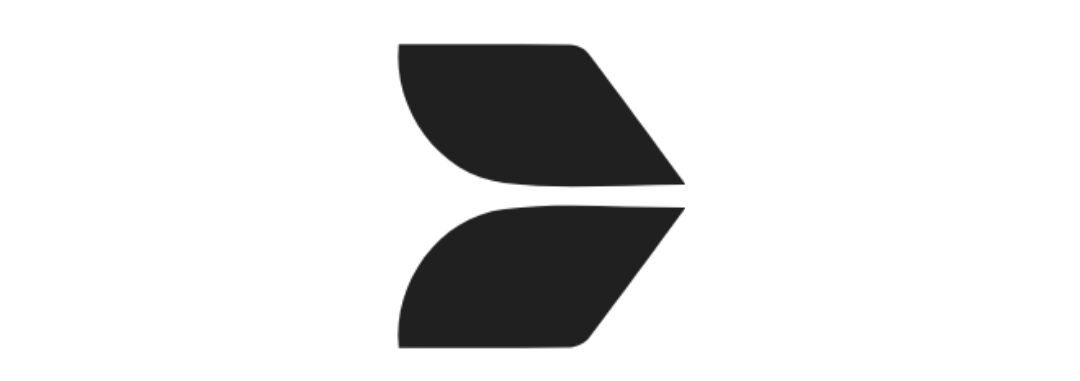 |
What’s next
Here’s what’s left before full-scale production:
- Submit remaining patent applications
- Finalize paddle graphics with our design agency
- Final compliance tests with NTS/Element
- Expanding tech to our elongated and widebody shapes
- Finishing design details like buttcap logos
- Receiving USAP approvals
- Confirming production flow for scalable output
- Building and purchasing equipment for production volumes of output
Once these steps are complete, we’ll move to launch the GT in all three shapes: hybrid, elongated, and widebody.
In the meantime, we’ll be doing a limited beta release later this month in just the hybrid shape. These beta units won’t be USAP-approved but will let early adopters experience the GT firsthand.
We’ll announce beta ordering info soon.
Thanks for your continued support and patience. We can’t wait to show you what Fusion Foam™ can really do.
As an IPTPA Level II instructor here in Birmingham, AL, I, along with many of my students, have really enjoyed the line of Spartus paddles. I have purchased and played with the Apollo, Olympus, and Oracle. They all perform exceptionally well and give my students a nice variety of quality and affordable choices. I am very excited to hear about the GT and look forward to its release. If I can assist in your beta program, please count me in. Thank you!
@Bobby Welch: Yes, the betas will be available to ambassadors first!
@Thomas Jackson: Thank you! The beta round will be opening shortly – we will send out more information soon.
Are embassoders gonna get first dibs?
The GT in the hybrid shape sounds truly amazing!!! I currently have a Honolulu J2FC+ on pre-order and after reading about your GT I would gladly cancel it if I can get get one of the beta units. I did buy an Apollo last year which I have enjoyed. Please let me know if I have any chance to get in the queue for one. Thanks so much!
Leave a comment